BENEFITS OF THE CEMENT SECTOR

Optimize dosing. Cost savings in raw materials.

Avoid and/or reducecyclon blockages. Lower clinker losses.

Optimize furnace operating conditions. Energy saving.

Control cement grinding (cold start of the mill).

Quality control of fine and additions (limestone, high furnace slag, fly ash, natural puzolanas, etc.).

Influence of secondary/alternative fuels on the process.

Reuse materials from electrofilters.

Predict final performance (settingtime, mechanical resistors, etc.).
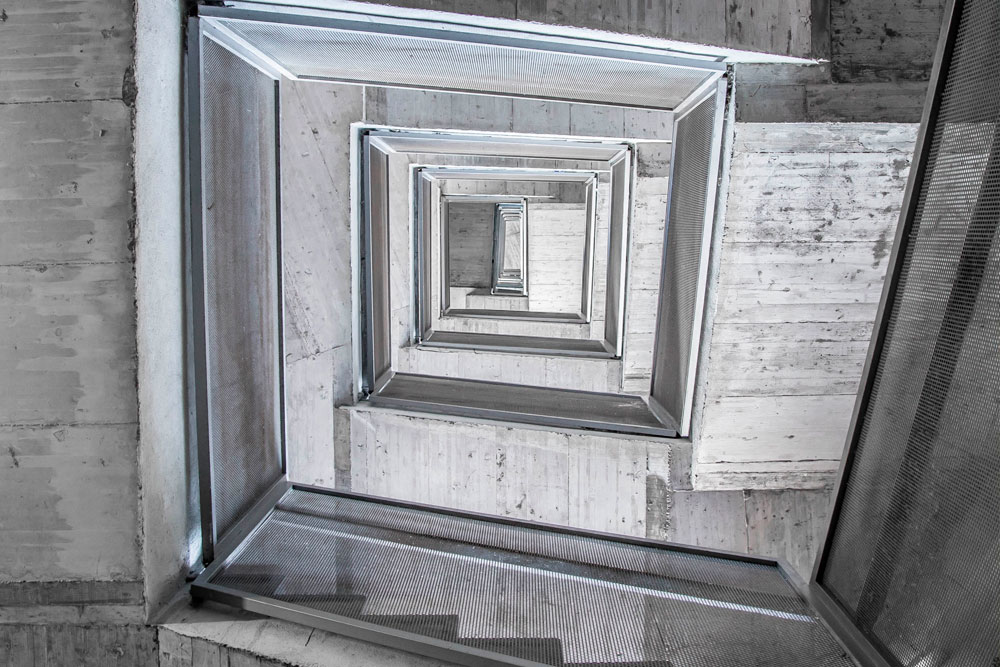
KNOW IN DETAIL WHAT BENEFITS WE CAN BRING TO THE CEMENT SECTOR
Commodity savings
By controlling the quality of raw materials by X-ray diffraction, it is possible to know their mineralogy and get to a correct dosage of them. This can lead to material savings and therefore cost savings.
Some of the analyses that can be carried out for the control of raw materials are:
– Determination of purity of limestone: by quantifying different carbonates (calcite, aragonite, dolomite, magnesite, ankerite, siderite, huntite, etc.), and by identifying and quantifying impurities such as pyrite.
– Determination of the purity of the sulfate source: by quantifying different sources (gypsum/anhydrite/basanite) that may affect differently the setting, the identification and quantification of other sulfates, e.g. celestine, and the identification and quantification of impurities, e.g. quartz, dolomite, feldspars.
Avoid and/or reduce cyclone blockages. (cyclon blockages)
By DRX monitoring the mineralogical composition of hot flour you can study the formation of phases that cause obstructions/accumulations in cyclones. This can lead to a balanced proportion of elements in hot flour that reduces the number of accumulations. This reduction of cyclone locks therefore reduces the loss of clineker associated with them.
Optimize furnace operating conditions
By monitoring by DRX the mineralogical composition of the clínker at the outlet of the furnace, it is possible to track the relationship of the different phases of the clínker, as well as its polymorphs. This can detect possible anomalies in the operation of the same, as well as the quality of the clycker.
It is possible to optimize the temperature of the furnace cooking area (BZT ) using the alita values determined by DRX.
Information from minority phases: Quartz and free lime: incomplete reactions in the oven.
In addition to the presence of some phases can give us problems in the finished product, such as:
Free lime and periclass: expansion problems;
Alkaline sulfates: Influence on setting properties.
The DRX study of the ferrite phase can provide information on the cooling speed of the clinker which in turn is important for understanding reactivity at an early age.
Cold start of the mill
The cement grinding process can be optimized by DRX by tracking the evolution of the gypsum/baseite/anhydrite content in the mill.
On the other hand, the influence of grinding additives on particle size can be studied using DRX.
Limestone, high furnace slag, fly ash, natural puzolanas, etc…
Through DRX it is possible to carry out not only the quantification of crystalline phases, but also an aefa phase. This is useful in the characterization of ash and slag-type additions as they are the main source of chemical reactivation and therefore improvements in final performance.
Within the quality control of fine it is important to highlight the monitoring or monitoring of breathable silica powder.
The use of alternative fuels can incorporate new elements (P, Zn, etc.) that stabilize different polymorphs in the clínker. It can also lead to the emergence of new minority phases in the clínker. Therefore, monitoring the mineralogical phases of the clínker can help the correct use of these alternative fuels and help obtain clínkers with reproducible properties.
Reuse materials from electrofilters.
Knowing the elemental and mineralogical composition of the material collected in the factory electrofilters allows its correct reintegration into the production process. In some countries the use of any powder used as a cement additive (<5% by weight) requires a detailed analysis of the mineral composition.
Daily monitoring of samples using different characterization techniques makes it possible to carry out an adequate correlation between composition and final properties of the material.